To explain the wide range of system functionality, let us recall
its concept and architecture of the software environment.
At the beginning of the development, there was a desire to use a
better system for creating custom application programs than the
so-called SCADA programs were and still remain. These programs are
considerably limited by their principles of operation, where a fixed
database loop is often cyclically serviced by a database of tags
(internal variables) and based on configuration data rendered an
operator graphical interface. The expression capabilities and
efficiency of such architectures cannot be high. SCADA programs can
serve well in the situations for which they were designed. But we want
more, today's IT world is rich and we need a freely programmable
system for our custom solutions. However, it is too laborious to
program every application from scratch, even if we take full advantage
of object-oriented programming languages.
If we take a closer look at the principles of most of today's
modern conceived program systems, we find that it is usually a
structure of program components that work together and communicate
with each other through defined program interfaces. The basic idea
behind the creation of the Control Web system is to create a set of
program components and then simply compose application programs from
instances of these components. The great strength of this concept in
Control Web is that the basic type of component we call a virtual
machine has no limitations in functionality and features, or in
quantity. The system does not know what all virtual instruments do -
in applications we use simple virtual instruments such as a button or
measuring instrument, as well as complex components such as a web
server, SQL database, stereoscopic camera or neural network. The
Control Web system only needs to be able to detect virtual appliance
components in external dynamic link libraries that are not limited in
their names or quantities again, and then manufacture component
instances and supply them for application program construction
purposes. Component instances exist in structures through which events
and data flow to which components respond. The structure of the
application program in the computer memory is thus practically
identical to the structure of a program that would be created in C ++.
Also, this program is comparatively powerful and efficient. It is
often more powerful as reusable components are carefully tuned and
optimized.
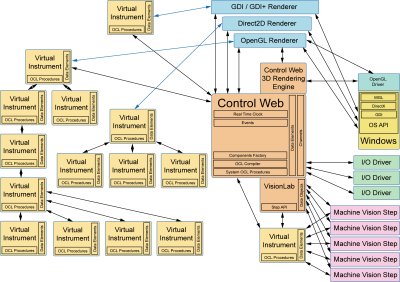
Structure of application components in Control Web
environment
In addition to identifying and instantiating usable components, the
Control Web core handles event distribution, including real time,
maintains global data element and channel data, and secures
communication in a networked environment.
The application program then consists of a structure of
components, which can be:
virtual instruments - their functionality is
virtually unlimited, they can do anything, and there are many such
instruments in applications
graphics renderers - for virtual machines, they
provide general abstract access to graphical features regardless of
the specific graphics API of the operating system
input / output device drivers - provide
communication with the outside world in the form of input and output
units, PLCs or software standards such as OPC UA etc.
machine vision steps - machine vision algorithms
above the image provided by camera virtual instruments
Při tvorbě aplikačního programu nejsme spoutání žádným předem
naprogramovaným systémem, vytváříme zcela unikátní vlastní strukturu
se svými algoritmy. To nám skýtá značné, prakticky neomezené možnosti.
Určité riziko spočívá pouze v tom, že náš program nebude dělat to co
chceme, ale pouze to, co jsme naprogramovali :-). Vždy ale vznikne
paměťově bezpečný a stabilní aplikační program. Můžeme velice
jednoduše tvořit programy v širokém rozsahu informačních a
automatizačních technologií. Nemusí to rozhodně být jen tradiční sběr
dat a operátorská rozhraní, ale mohou to být např. webové aplikace
včetně redakčního rozhraní, databázové aplikace se vstupními formuláři
a výstupními sestavami, aplikace přímého řízení strojů a výrobních
linek v reálném čase, aplikace kamerového dohledu, vizuální inspekce a
komplexní systémy strojového vidění a mnoho dalšího. Fantazie tvůrců
aplikací není nijak omezována. Přitom většinu vývoje lze udělat pouze
pomocí myši v grafickém vývojovém prostředí. Především však můžeme
vytvářet spoustu velmi rozdílných aplikací v jednom vývojovém
prostředí. Ušetříme spoustu práce a času - nemusíme se učit několik
programovacích standardů a nemusíme ovládat několik programů a
konfiguračních nástrojů.
Applications are built according to the principles now
promoted as Industry 4.0
It is quite interesting that many of the concepts for building
smart production systems, today as popular as Industry 4.0, have
been part of the Control Web architecture for a long time.
Here are some examples:
cloud and Internet of services - more than
twenty years ago, as the Control Web name suggests, both the Web
client and the server were part of the system, allowing access
to dynamic application data through Web services. The system was
designed from the outset for applications dispersed in TCP / IP
networks. It enables unified access to local data and data
anywhere in the computer network. 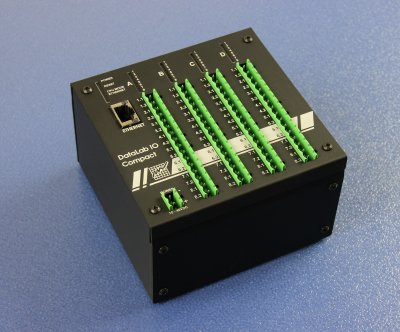
DataLab industrial I/O unit with Ethernet
connection to TPCP/IP network
Industrial Internet of Things - the concept
of a computer is much wider than it was in the past, as it is
part of many common devices. Your computer may have a credit
card size and run Control Web. Such a device is then easily
integrated into the Internet of Things. Also, industrial DataLab
I/O units can be connected to a TCP/IP network and can be
located anywhere. E.g. the entire industrial automation
switchboard of a machine or production line can be integrated
into the system via a single Ethernet connection. 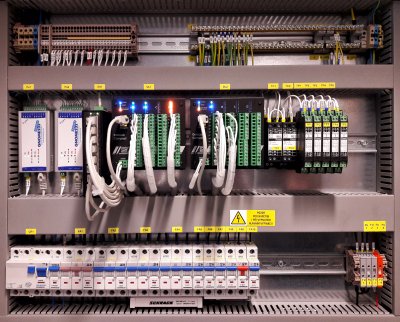
Obr 3: Automatizační rozvaděč lze díky jednotkám
DataLab připojit do počítačové sítě
virtual reality and digital models -
Although the 3D rendering system was not available immediately
from the first version of the system, in 2002 it was probably
the first before other industrial automation systems. Now in the
latest version of the system, the idea of hybrid virtual
instruments has been fully completed and implemented, which can
exist both in the three-dimensional space of the scene, as well
as in conventional panels with arbitrary graphics renderers. All
spatial visualizations can also be visualized through
stereoscopic virtual reality glasses. 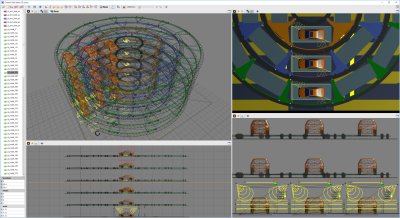
Scene preparation in 3D editor - spatial models of
real devices, machines and buildings are clearer and clearer
in some applications than area diagrams
cybernetic — physical systems - a device in
which Control Web is running is no longer a simple programmable
controller. In addition to controlling the machine, it can
provide the machine with a perception of the outside world
through machine vision, connect with other information systems,
databases, communicate on the Internet and make decisions using
artificial intelligence. 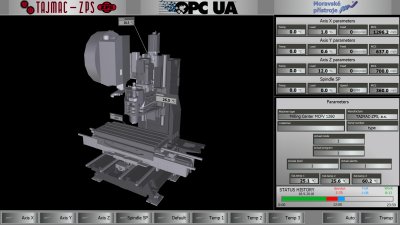
In a smart factory, each machine is part of a
computer network
Thanks to its network and communication, database and
visualization capabilities, Control Web maximally supports the
progressive way of controlling industrial production and
management of production equipment and machines as well as control
and automation systems solutions.
Effective solution of control and automation systems
If we have a control unit with the Control Web system in the
automation system, we can design the entire system as efficiently
as possible. For many systems, we will need nothing but a control
computer and some industrial inputs and outputs. Everything can
run in a single programming environment, so we save money not only
on PLC, but above all, we will greatly simplify and speed up
programming. In all cases, of course, you cannot do without a PLC,
but in many cases it is. When upgrading older industrial
automation systems, we often replace several PLCs with a new
control computer with new software, and at a lower cost we get
higher performance and an incomparably higher range of
functionality.
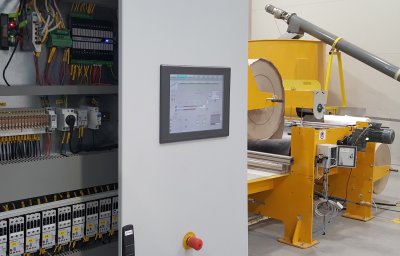
Efficient automation of the production line with
Control Web - a computer with a graphical interface for the
operator and DataLab unit for machine control connected via
Ethernet
Especially significant efficiency gains are obtained in cases
where visual inspection cameras are also used. Combining machine
vision and visual inspection with all the features of the Control
Web programming environment is a high value for a smart
statement.
Open standards bring the freedom and easier maintenance and
further development
The architecture of the Control Web system is based on the use
of open standards of information technology. Reduces the risk of
being hostage providers who often use your own, closed, and
possibly world-protected communication systems, data and program
standards that are available for long-term customer attachment to
their customers. Users will then become safe hostages of these
suppliers. The efforts of large, unnamed, well-known concerns to
lock suppliers are no less intense than in the past. Only before
have all been made available openly and straightforwardly, while
more hidden and sophisticated methods can be chosen today - and
when it is possible to declare what advocates of open standards
you can now be modern and look good to say.
Developing, repairing and maintaining applications is
completely free
So we still need to invest some of our own work to create an
application program, but the development environment, including
all add-ons and extensions, is available for free. We can also
download and use any driver as well as VisionLab vision system. We
will only need a license when we deliver it to the end customer
and deploy our application into continuous operation.
Without the need to invest in any equipment, we can try what we
can create with the help of Control Web.
Roman Cagaš
|