Courtesy of the owner we can introduce a successful solution of the
complete digitization of the factory production of traditional
plastics processor, the company Auttep Ltd. Although there are
production lines and plants that have been built on the "greenfield"
and have been fully automated and interconnected from the start, the
vast majority of industrial plants have been evolving for a long time.
Therefore, it is common to have machines of different age and
different equipment side by side in production halls. A machine whose
capacity and quality of production is still sufficient is usually not
wise to throw away simply because it has served us well for several
decades. Here is an example how to effectively digitize production
where high-performance and modern machines stand side by side, along
with machines and other technologies that were not initially foreseen
for inclusion in communications networks.
The system provides many functionalities of modern
digitized production:
receipt and delivery of material from stock using mobile
terminals
automatic control of the pallet transport system connected to
the storage area
monitoring operating states, duty cycles and functions of all
machines
lighting control according to movement of persons in
halls
control of heating of production halls by gas-fired heating
units
detection of movement of persons in doors, gates and in
individual sectors of the area
door and gate monitoring and control
panoramic camera management and transmission of image data in
the system as required by operators
power consumption measurement
two redundant servers that back up each other, including SQL
server data replication
the system also allows authorized persons to remote access to
all functions
Portable terminals make it easy to pick up goods from the warehouse
by picking up barcodes. They also run applications in the Control Web
environment. The applications are operated via touch screens and have
a simple and clear graphical user interface. Goods are transported by
elevator on several floors. Throughout the premises the terminals are
connected wirelessly via Wi-fi. The supplier of the pallet transport
system is TMT spol. s.r.o., Chrudim.
The basis of the system functionality is two redundant servers and
a communication structure. Both servers run the same applications in
the Control Web network environment. In case of downtime or failure of
one server, the whole system continues to run without any
restrictions. Also, data on SQL servers is replicated between two
computers. The system is hidden from the outside world behind a
firewall. A richly dimensioned distribution of Ethernet connections is
then available throughout the plant. Mains switches are safely housed
in the switch cabinet always high on the walls of the production
halls. Due to their location, they also do not interfere with
anything.
An interesting feature, as well as a demonstration of the
flexibility and functionality of the DataLab units, is the elegance
and simplicity with which older production date machines are connected
to the network monitoring and control system.
The DataLab Compact units also controls hot air units and hall
doors and gates.
The compact Datalab units take up very little space. They can also
be placed in the switchboards of modern machines without any
problems.
Machine vision VisionLab, integrated into the Control Web
environment, detects the movement of people in entrances to the halls
and in selected areas using camera images. The cameras are also
connected to the TPCP / IP network via Ethernet cables.
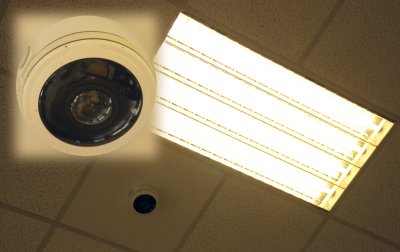
Panoramic cameras are usually located on the ceiling of the
halls
The described production digitization system uses exclusively
DataLab units with Ethernet connection, but there are also units for
remote connections via RS485 and especially units with USB interface.
These can be advantageously used for direct machine control due to the
high data throughput and short response time.
The principles underlying the described factory digitization
solution demonstrate the efficiency and effectiveness of using
DataLabs with Ethernet connections on a TCP / IP network, as well as
the versatility and scalability of the Control Web programming
environment. The whole system is a good investment for the future as
it is permanently open and allows the integration of new devices,
communication protocols and other software. This solution thus
fulfills the principles often referred to as Industry 4.0.
RC
|