This interconnection within one program environment significantly
simplifies not only the development of new applications, but also the
resulting solution is cheaper than other concepts. In most cases, we
can use a single computer to which both cameras and industrial input /
output units are connected and which is also connected to a computer
network and company information system. This computer usually runs the
graphical user interface of the application, the database SQL server,
the web server, visual inspection and machine vision tasks, as well as
the entire logic of the automation application.
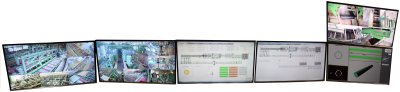
Fig. 1: Machine vision as part of the control system. The
range of functionality makes Control Web an effective industry
digitization tool for virtually any customized solution.
If additional remote automation racks are needed, each can be
connected via Ethernet and TCP/IP networks. An example of such a
remote switchboard is shown in Fig. 2. The efficiency of the solution
and the advantageous price of all hardware and software is obvious in
such conceived systems.
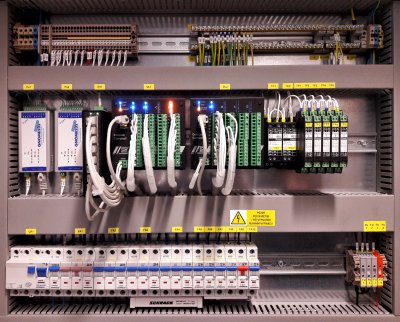
Fig. 2: The automation switchboard is connected with a
single Ethernet cable thanks to DataLab units with TCP/IP
protocol.
With the advent of the new generation of Control Web 8, several
features have been added to further enhance machine vision integration
capabilities.

Fig. 3: Demonstration of stereoscopic capturing of outdoor
scene space. The virtual instrument builds a 3D model of the sensed
space and it can determine eg. the position of cars and their
distance from the camera.
A new type of data data objects for transferring general binary
data has been added to machine vision. This type corresponds to data
elements of the data type in the Control Web environment. Virtual
instruments in the application program and steps in the machine vision
chain can now efficiently exchange blocks of arbitrary data. The type
of data and the format of its storage is not prescribed in any way. In
some tasks, such as further work with detected significant image
points in an application program, this technique of transferring
binary data blocks brings significant acceleration. New possibilities
of cooperation of automation application with a chain of machine
vision steps can be well demonstrated eg by virtual instruments for
displaying spatial scene in the form of 3D object. The image data is
captured by a stereoscopic pair of cameras. This virtual instrument
has several peculiarities. It depicts a scene captured by cameras, but
does not communicate directly with the cameras itself. It needs not
only two images from cameras, but also information about feature
points and their descriptors found in these two images. It must
therefore cooperate with machine vision, which, by means of the point
detection step, fills data elements of the data type with found
descriptors of these points. Similar to the point descriptors, the
actual image from each camera is transmitted to the virtual instrument
via data elements of the data type. A virtual instrument can be very
useful in applications where we need information about the distances
of objects in an image, when we have to find objects at different
distances or avoid collisions with objects in space while moving. By
means of data elements of the data type, any image can also be
transmitted, for example, to display devices located anywhere in the
3D space of the scene.
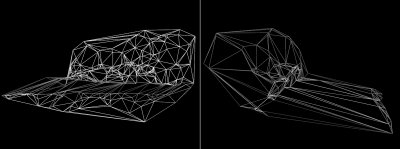
Fig. 4: 3D model of the captured scene, created from two
camera images
We can also use VisionLab's ability to locate feature image points
and calculate descriptors describing their surroundings efficiently
and with maximum use of massively parallel GPU performance, to detect
general objects in images. Feature points are searched on a scale of
several scales, then objects can be detected independently of their
rotation and brightness, but also independently of their size. A set
of descriptors that characterize objects that we want to identify
further in the image data can provide detection steps in both files
and data elements of the data type.
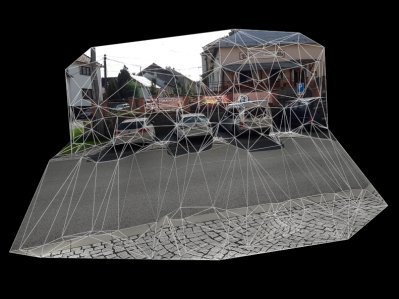
Fig. 5: In 3D space model it is possible to measure
distances of individual surfaces from cameras
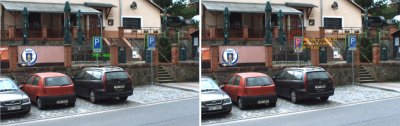
Fig. 6: Via the detected feature points, eg. traffic signs
can be identified in the camera image
Now that the new eighth generation of Control Web is available, it
is also worth noting that the development version of Control Web can
be downloaded free of charge from www.controlweb.eu and used on an
unlimited number of free installations. The license is only required
if the application is required to run continuously. All VisionLab
drivers and vision systems can be used as well.
Roman Cagaš
|